
In 4 Schritten von der Kohlenstoff- oder Glasfaser zum fertigen Bauteil
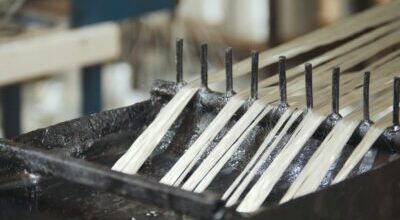
Faserhaltige Verbundwerkstoffe werden weitreichend in verschiedenen Industrien eingesetzt. Die Einsatzgebiete sind umfassend und reichen von der Automobil und Luftfahrt, über Windenergieanlagen und Sportgeräte bis hin zum Bauwesen.
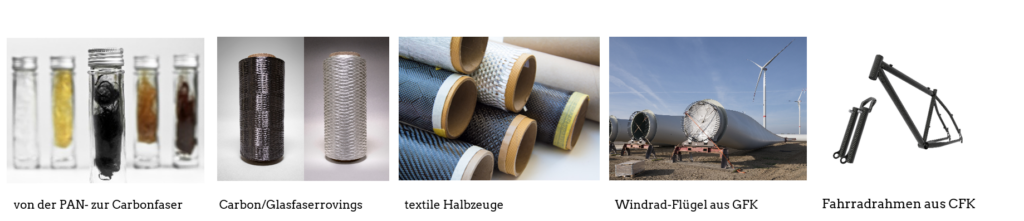
Schritt 1: Gewinnung der Ausgangsstoffe
Gewinnung der Ausgangsstoffe: Der Ausgangsstoff der Fasern für Faserverbundwerkstoffe ist zumeist Kohlenstoff (für Carbonfasern) oder Glas (für Glasfasern). Gegenwärtig wird der Kohlenstoff aus Erdöl gewonnen, dagegen setzt sich das Glas in Abhängigkeit der Eigenschaft aus mehreren Rohstoffen (Quarzsand, Kalk etc.) zusammen [1], [2].
Schritt 2: Fertigung von Fasern und Garnen
Für die Herstellung von Carbonfasern wird das Ausgangsmaterial Polyacrylnitril (PAN) in mehreren Prozessschritten mit verschiedenen Temperatur- und Druckverhältnissen verarbeitet (Carbonisierung und Graphitierung). Daraus gehen Fasern aus fast reinem Kohlenstoff hervor. Die Herstellung von Glasfasern erfolgt über das Schmelzen der Ausgangsstoffe. Die Glasschmelze wird durch feine Düsen geführt, sodass feine Glasfasern entstehen. Anschließend werden sowohl bei Carbon- als auch bei Glasfasern die einzelnen Fasern in mehreren Bündeln (Rovings) zusammengefasst und auf Spulen gewickelt [1].
Schritt 3: Fertigung von faserhaltigen Halbzeuge
Für die Herstellung von mattenförmigen Bewehrungen werden die Rovings in textiltechnologischen Prozessen verarbeitet und dabei mit einer Kunststoffmatrix getränkt. Für die Herstellung von faserhaltigen Geweben und Vliesstoffen werden die Fasern in unterschiedlichen Richtungen zueinander ausgelegt und mithilfe eines Kettfadens nach konkreten, vorab definierten Mustern fixiert. Durch die Zugabe eines Härters und die Erwärmung entstehen flächige Gelege bzw. Gewebe, die schließlich auf die entsprechende Breite zugeschnitten und aufgerollt werden [1].
Dagegen werden stabförmige Bewehrungen im Strangziehverfahren bzw. durch die sogenannte Pulltrusion hergestellt. Dabei werden einzelne faserhaltige Bündel direkt zu Stäben zusammengeführt und mit Harzen oder thermoplastischen Kunststoffen imprägniert. Es ist üblich, die Stäbe zur besseren Haftungsvermittlung durch Fräsen zu profilieren oder Rippen auf die Stäbe aufzubringen [2].
Schritt 4: Herstellung von Bauteilen aus Faserverbundwerkstoffen
Im Bauwesen können mit den matten- oder stabförmigen Strukturen neue Bauteile der Carbon- oder Textilbetonbauweise in Betonfertigteilwerken hergestellt werden. Werden bestehende Stahlbetonbauwerke mit Carbon- oder Textilbeton verstärkt oder instandgesetzt, erfolgt dies direkt vor Ort auf der Baustelle [3], [4].
In anderen Branchen werden Bauteile (Rotorblätter, Tennisschläger etc.) aus flächigem Gewebe beispielsweise mittels der Verfahren Preforming oder Nasspressen in der Fläche und Formgebung hergestellt. Mittels mechanischer Nachbearbeitung erhalten die ausgehärteten faserhaltigen Bauteile ihre endgültigen Konturen, Bohrungen und Ausschnitte [5].
Schlussfolgerung
Die Nutzung solch eines leistungsstarken und gleichzeitig energieintensiven Produktes macht es umso bedeutender, dass am Ende der Nutzungsdauer die wertvollen Rohstoffe in den Stoffkreislauf zurückgeführt oder in neue Anwendungsfelder überführt werden. Auf diese Weise ergeben sich vielfältige Möglichkeiten, an neuen Wertschöpfungsketten teilzunehmen.
Stand 2021-06-21
Quellenverzeichnis
[1] Schürmann, H. (2007). Konstruieren mit Faser-Kunststoff-Verbunden: Mit 39 Tabellen (2., bearb. und erw. Aufl). Springer.
[2] Mathes, V., Witten, E., & AVK, Industrievereinigung Verstärkte Kunststoffe (Ed.). (2014). Handbuch Faserverbundkunststoffe/Composites: Grundlagen, Verarbeitung, Anwendungen (4th ed.). Springer Vieweg. 378-390.
[3] Kirsten, M., Freudenberg, C., & Cherif, C. (2015). Carbonfasern, der Werkstoff des 21. Jahrhunderts: Textile Ausgangsbasis für filigrane hochtragende Betonbauteile. Beton- und Stahlbetonbau, 110(S1), 8–15. https://doi.org/10.1002/best.201400105
[4] Scheerer, S., Schladitz, F., & Curbach, M. (2015). Textile reinforced Concrete – From the idea to a high performance material. In Brameshuber, Wolfgang (Ed.), Proceedings of the FERRO-11 and 3rd ICTRC in Aachen.
[5] Mathes, V., Witten, E., & AVK, Industrievereinigung Verstärkte Kunststoffe (Ed.). (2014). Handbuch Faserverbundkunststoffe/Composites: Grundlagen, Verarbeitung, Anwendungen (4th ed.). Springer Vieweg. 311-346/502-536.
Zur Partnerschaft
Seien Sie Teil des Bündnisses und stellen Sie sich mit uns gemeinsam den Herausforderungen in Hinblick auf den nicht mehr zu vermeidenden Umgang mit Faserverbundwerkstoffen. Lassen Sie uns gemeinsam die Region „Elbtal Sachsen“ in eine wirtschaftlich widerstandsfähige Zukunft führen.