
Alternative approaches to carbon fiber production
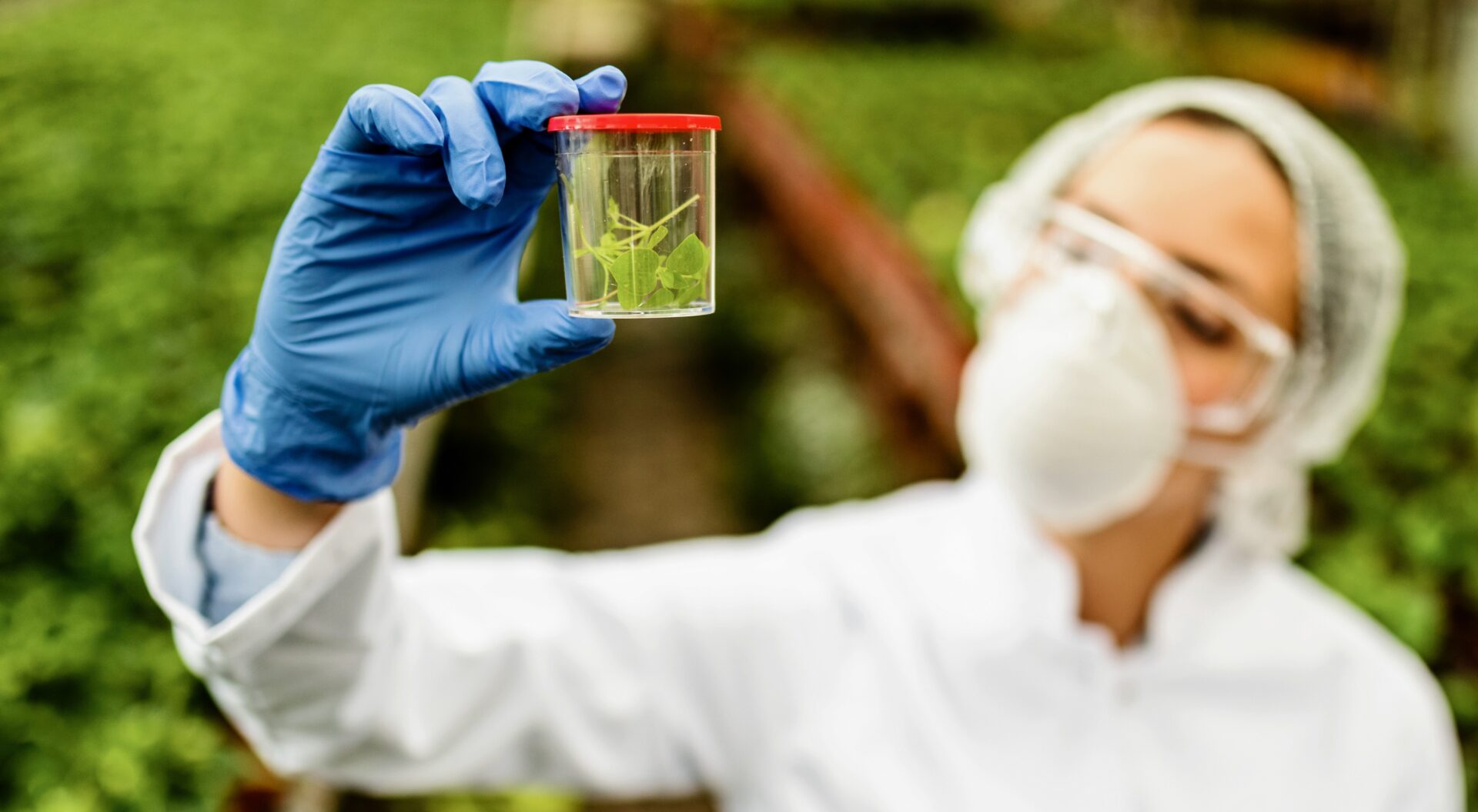
Currently, the production of carbon fibers is still dependent on fossil fuels, which involve significant CO2 emissions during extraction and processing. As the use of carbon fibers increases, so does the responsibility to utilize both secondary and environmentally friendly resources in their production. In addition to using recycled fibers, there are currently four promising approaches to reduce the dependence on fossil fuels in carbon fiber production.
Algae
Algae, or microalgae, grow approximately 10 to 50 times faster than land plants and can accumulate up to 70% weight lipids or cell dry weight, making them an optimal CO2 sink [1, 2, 3]. Lipid-rich algal biomass is used for carbon fiber production [4]. The CO2 stored in algae is bound in the form of sugars and algae oil [5]. Through chemical and biotechnological processes, new raw materials for various industrial processes can be obtained from these sources. A unique advantage is the utilization of non-arable land, avoiding conflicts with food production or other technical infrastructures [4].
CO2
Presently, using CO2 as a material for carbon fibers involves capturing carbon dioxide from the air [6], exposing large volumes of air to sorbents [7], and electrochemically converting it into carbon [8]. Recent findings indicate that using molten lithium carbonate with dissolved lithium oxide for the reaction and deposition of airborne carbon dioxide is feasible and cost-effective [9]. Another approach is the continuous direct decomposition of CO2 into solid carbon and oxygen using a liquid metal alloy [10].
Lignin
Lignin is a byproduct of the paper and pulp industry and a natural component of wood and other plant materials. It consists of aromatic macromolecules [11, 12] and can be converted into carbon at high temperatures and in the absence of oxygen [13]. Due to its high carbon content and biological renewability, a significant portion of CO2 emissions that occur during the production of petroleum-based polymers can be avoided [14]. Although some companies have offered products made from lignin-based carbon fibers since the 1970s [15], the majority of lignin is still directly burned for electricity generation [14].
Polyethylene
Polyethylene has gained significant attention for carbon fiber production due to its favorable mechanical properties, high carbon content (86%), ability to be melt-spun at high production rates, easy availability, relatively low costs, easy deformability, and high carbon yield during conversion into carbon fibers [16, 17, 18]. To convert polyethylene into carbon fibers, it is first processed into a carbon precursor by pyrolyzing it in an inert atmosphere at high temperatures [18, 19]. Comprehensive studies on the pyrolysis of carbon precursors have been conducted by the Technical University of Hamburg [20]. This method holds great potential for utilizing plastic waste as feedstock [19].
Alternatives
Identifying environmentally friendly resources for carbon fiber production presents an attractive research and development field.Identifying environmentally friendly resources for carbon fiber production presents an attractive research and development field. The challenge is how to design processes along the value chain to be both effective and efficient.
In addition to the mentioned approaches, bio-based materials also hold significant potential for carbon fiber production. However, typically only about 10 to 30 weight percent of processed biomass can be converted into carbon fibers, as the content and orientation of ordered carbon structures need to be increased [21]. Furthermore, there are initial attempts to extract carbon fibers from rayon and glycerin, with rayon alone having lower strength than required for most structural applications. Additionally, there is low yield and high cost. The use of glycerin, in turn, requires direct ammonoxidation, which is still uneconomical [22].
As of 2024-01-08
List of references
[1] Batista, A. P., Ambrosano, L., Graça, S., Sousa, C., Marques, P. A. S. S., Ribeiro, B., Botrel, E. P., Castro Neto, P., & Gouveia, L. (2015). Combining urban wastewater treatment with biohydrogen production – An integrated microalgae-based approach. Bioresource Technology, 184, 230–235. https://doi.org/10.1016/j.biortech.2014.10.064
[2] Khoo, K. S., Chew, K. W., Yew, G. Y., Leong, W. H., Chai, Y. H., Show, P. L., & Chen, W.-H. (2020). Recent advances in downstream processing of microalgae lipid recovery for biofuel production. Bioresource Technology, 304, 122996. https://doi.org/10.1016/j.biortech.2020.122996
[3] Arnold, U., Brück, T., De Palmenaer, A., & Kuse, K. (2018). Carbon capture and sustainable utilization by algal polyacrylonitrile fiber production: process design, techno-economic analysis, and climate related aspects. Ind. Eng. Chem. Res., 57(23), 7922–7933. https://doi.org/10.1021/acs.iecr.7b04828
[4] TU München. (2019). Innovative Materialien mit Carbonfasern aus Algen. URL: https://www.ch.tum.de/ch/forschung/highlights/archiv-2019/innovative-materialien-mit-carbonfasern-aus-algen
[5] Darzins, A., Pienkos, P., & Edye, L. (2010). Current status and potential for algal biofuels production. A report to IEA Bioenergy Task, 39(13), 403–412.
[6] Sujan, A. R., Pang, S. H., Zhu, G., Jones, C. W., & Lively, R. P. (2019). Direct CO2 capture from air using poly(ethylenimine)-loaded polymer/silica fiber sorbents. ACS Sustainable Chem. Eng., 7(5), 5264–5273. https://doi.org/10.1021/acssuschemeng.8b06203
[7] Gambhir, A., & Tavoni, M. (2019). Direct air carbon capture and sequestration: how it works and how it could contribute to climate-change mitigation. One Earth, 1(4), 405–409. https://doi.org/10.1016/j.oneear.2019.11.006
[8] Lin, R., Guo, J., Li, X., Patel, P., & Seifitokaldani, A. (2020). Electrochemical reactors for CO2 conversion. Catalysts, 10(5), 473. https://doi.org/10.3390/catal10050473
[9] Ren, J., Li, F.-F., Lau, J., González-Urbina, L., & Licht, S. (2015). One-Pot Synthesis of Carbon Nanofibers from CO2. Nano Lett., 15(9), 6142–6148. https://doi.org/10.1021/acs.nanolett.5b02427
[10] Zuraiqi, K., Zavabeti, A., Clarke-Hannaford, J., Murdoch, B. J., Shah, K., Spencer, M. J. S., McConville, C. F., Daeneke, T., & Chiang, K. (2022). Direct conversion of CO2 to solid carbon by Ga-based liquid metals. Energy & Environmental Science, 15(2), 595–600. https://doi.org/10.1039/D1EE03283F
[11] Mili, M., Hashmi, S. A. R., Ather, M., Hada, V., Markandeya, N., Kamble, S., Mohapatra, M., Rathore, S. K. S., Srivastava, A. K., & Verma, S. (2022). Novel lignin as natural‐biodegradable binder for various sectors—A review. Journal of Applied Polymer Science, 139(15), 51951. https://doi.org/10.1002/app.51951
[12] Behr, A., & Seidensticker, T. (2018). Einführung in die Chemie nachwachsender Rohstoffe: Vorkommen, Konversion, Verwendung. https://doi.org/10.1007/978-3-662-55255-1
[13] Frank, E., Steudle, L. M., Ingildeev, D., Spörl, J. M., & Buchmeiser, M. R. (2014). Carbonfasern: Präkursor-Systeme, Verarbeitung, Struktur und Eigenschaften. Angew. Chem., 126(21), 5364–5403. https://doi.org/10.1002/ange.201306129
[14] Wang, S., Bai, J., Innocent, M. T., Wang, Q., Xiang, H., Tang, J., & Zhu, M. (2022). Lignin-based carbon fibers: Formation, modification and potential applications. Green Energy & Environment, 7(4), 578–605. https://doi.org/10.1016/j.gee.2021.04.006
[15] Black, S. (2016). Alternative precursor R&D: What are the alternatives to PAN? URL: https://www.compositesworld.com/articles/alternative-precursor-rd-what-are-the-alternatives-to-pan
[16] Zhang, D. (1993). Carbon fibers from oriented polyethylene precursors. Journal of Thermoplastic Composite Materials, 6(1), 38–48. https://doi.org/10.1177/089270579300600104
[17] Eun, J. H., & Lee, J. S. (2021). Study on polyethylene-based carbon fibers obtained by sulfonation under hydrostatic pressure. Sci Rep, 11(1), 18028. https://doi.org/10.1038/s41598-021-97529-4
[18] Zhang, D., & Sun, Q. (1996). Structure and properties development during the conversion of polyethylene precursors to carbon fibers. J. Appl. Polym. Sci., 62(2), 367–373. https://doi.org/10.1002/(SICI)1097-4628(19961010)62:2<367::AID-APP11>3.0.CO;2-Z
[19] Yaqoob, L., Noor, T., & Iqbal, N. (2022). Conversion of plastic waste to carbon-based compounds and application in energy storage devices. ACS Omega, 7(16), 13403–13435. https://doi.org/10.1021/acsomega.1c07291
[20] Marcilla, A., Ruiz-Femenia, R., Hernández, J., & García-Quesada, J. C. (2006). Thermal and catalytic pyrolysis of crosslinked polyethylene. Journal of Analytical and Applied Pyrolysis, 76(1–2), 254–259. https://doi.org/10.1016/j.jaap.2005.12.004
[21] Fraunhofer Institute for Applied Polymer Research IAP. (2019). Bio-based carbon fibers – high performance and sustainability for light-weight applications. URL: https://www.iap.fraunhofer.de/en/press_releases/2019/biobased-carbon-fibers.html
[22] Milbrandt, A., & Booth, S. (2016). Carbon fiber from biomass. Clean Energy Manufacturing Analysis Center (CEMAC). URL: https://www.nrel.gov/docs/fy16osti/66386.pdf
About the partnership
Be part of the alliance and join us in facing the challenges with regard to the no longer avoidable handling of fibre composites. Let us together lead the region “Elbe Valley Saxony” into an economically resilient future.