
Alternative Ansätze zur Herstellung von Kohlenstofffasern
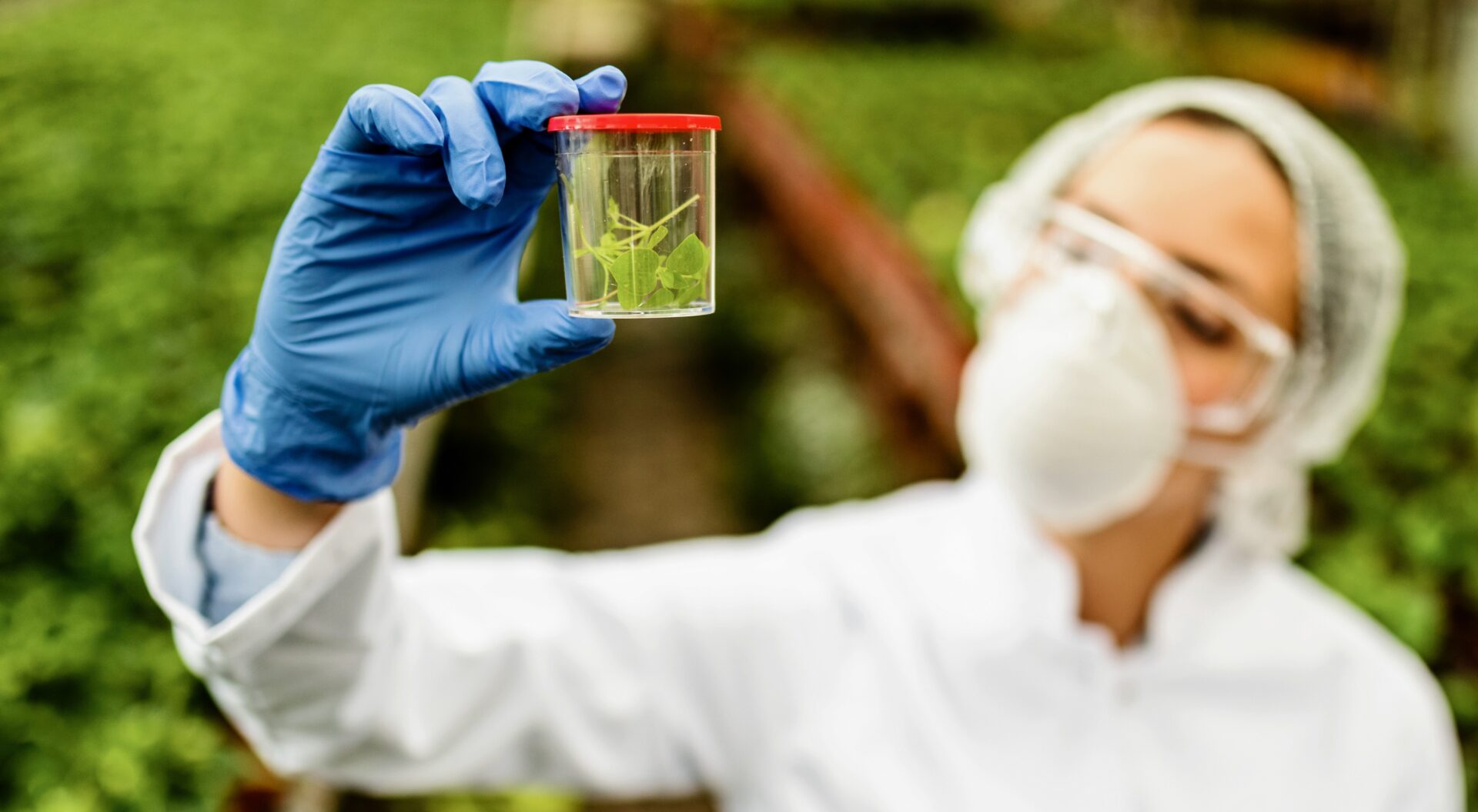
Gegenwärtig ist die Herstellung von Kohlenstofffasern noch immer abhängig von fossilen Brennstoffen, deren Abbau und Verarbeitung eine hohe CO2-Emission nach sich zieht. Mit dem zunehmenden Einsatz von Kohlenstofffasern steigt auch die Verantwortung, künftig sowohl sekundäre als auch umweltverträgliche Rohstoffe einzusetzen. Neben dem Einsatz recycelter Fasern gibt es gegenwärtig vier vielversprechende Ansätze, bei der Herstellung von Kohlenstofffasern die Abhängigkeit von fossilen Brennstoffen zu verringern.
Algen
Algen bzw. Mikroalgen wachsen etwa 10 bis 50mal schneller als Landpflanzen und können bis zu 70 % Gewichtslipide bzw. Zelltrockengewicht anreichern, wodurch sie eine optimale CO2-Senke darstellen [1, 2, 3]. Für die Herstellung von Kohlenstofffasern werden lipidreiche Algenbiomassen genutzt [4]. Das in Algen gespeicherte CO2 wird unter anderem in Form von Zuckern und Algenöl gebunden [5]. Aus diesen können mit chemischen und biotechnologischen Prozessen neue Ausgangsstoffe für verschiedenste industrielle Prozesse gewonnen werden. Eine Besonderheit besteht darin, nicht bebaubare Flächen nutzen zu können, um beispielsweise Konflikte mit der Produktion von Nahrungsmitteln oder anderen technischen Infrastrukturen zu vermeiden [4].
CO2
CO2 als Ausgangsmaterial für Kohlenstofffasern bedarf gegenwärtig das Auffangen von Kohlendioxid aus der Luft [6], indem große Luftmengen in Kontakt mit Sorptionsmitteln gebracht werden [7] und elektrochemisch in Kohlenstoff umgewandelt werden [8]. Jüngste Erkenntnisse zeigen, dass die Verwendung von geschmolzenem Lithiumcarbonat und darin gelöstem Lithiumoxid zur Reaktion und Abscheidung von Kohlendioxid in der Luft machbar und kostengünstig ist [9]. Ein weiterer Ansatz ist die kontinuierliche direkte Zersetzung von CO2 zu festem Kohlenstoff und Sauerstoff durch Verwendung einer Flüssigmetalllegierung [10].
Lignin
Lignin ist ein Nebenprodukt der Papier- und Zellstoffindustrie und ein natürlicher Bestandteil von Holz und anderen pflanzlichen Materialien. Dieses besteht aus aromatischen Makromolekülen [11, 12] und ist in der Lage, bei hohen Temperaturen und in Abwesenheit von Sauerstoff zu Kohlenstoff umgewandelt zu werden [13]. Aufgrund des hohen Kohlenstoffgehaltes und der biologischen Erneuerbarkeit kann ein erheblicher Teil der CO2-Emissionen – die sonst bei der Herstellung von erdölbasierten Polymeren entstehen – vermieden werden [14]. Obwohl bereits seit den 1970er Jahren immer wieder Mal einzelne Unternehmen Produkte aus ligninbasierten Kohlenstofffasern anbieten [15], wird immer noch der größte Teil des Lignins direkt zur Stromerzeugung verbrannt [14].
Polyethylen
Polyethylen hat aufgrund seiner guten mechanischen Eigenschaften, seines hohen Kohlenstoffgehalts (86%), seiner Fähigkeit, bei hohen Produktionsraten schmelzgesponnen zu werden, seiner leichten Verfügbarkeit, seiner relativ niedrigen Kosten, seiner leichten Verformbarkeit und seiner hohen Kohlenstoffausbeute bei der Umwandlung in Kohlenstofffasern große Aufmerksamkeit auf sich gezogen [16, 17, 18]. Um Polyethylen in Kohlenstofffasern umzuwandeln, wird es zunächst zu einem Kohlenstoff-Präkursor verarbeitet, indem es in einer inerten Atmosphäre bei hohen Temperaturen pyrolysiert wird [18, 19]. Umfassende Studien zur Pyrolyse von Kohlenstoff-Präkursoren wurden von der Technischen Universität Hamburg durchgeführt [20]. Dieses Verfahren bietet ein großes Potenzial für die Verwendung von Abfällen auf Kunststoffbasis als Ausgangsmaterial [19].
Alternativen
Die Identifikation von umweltverträglichen Rohstoffen für die Herstellung von Kohlenstofffasern stellt ein attraktives Forschungs- und Entwicklungsumfeld dar. Die Frage ist, wie Prozesse entlang der Wertschöpfungskette so gestaltet werden können, dass sie sowohl effektiv als auch effizient sein werden.
Neben den bisherigen Ansätzen weisen auch Biowerkstoffe ein sehr großes Potenzial für die Herstellung von Kohlenstofffasern auf. Jedoch können bisweilen nur etwa 10 bis 30 Gewichtsprozent der verarbeiteten Biomasse zu Kohlenstofffasern verarbeitet werden, zumal der Anteil und die Ausrichtung an geordneten Kohlenstoffstrukturen erhöht werden müssen [21]. Darüber hinaus gibt es auch erste Ansätze zur Gewinnung von Kohlenstofffasern aus Rayon und Glycerin, wobei allein Rayon eine geringere Festigkeit hat, als für die meisten strukturellen Anwendungen erforderlich ist. Zudem gibt es eine niedrige Ausbeute und zu hohe Kosten. Der Einsatz von Glycerin erfordert wiederum eine direkte Ammoxidation, die noch unwirtschaftlich ist [22].
Stand 2024-01-08
Quellenverzeichnis
[1] Batista, A. P., Ambrosano, L., Graça, S., Sousa, C., Marques, P. A. S. S., Ribeiro, B., Botrel, E. P., Castro Neto, P., & Gouveia, L. (2015). Combining urban wastewater treatment with biohydrogen production – An integrated microalgae-based approach. Bioresource Technology, 184, 230–235. https://doi.org/10.1016/j.biortech.2014.10.064
[2] Khoo, K. S., Chew, K. W., Yew, G. Y., Leong, W. H., Chai, Y. H., Show, P. L., & Chen, W.-H. (2020). Recent advances in downstream processing of microalgae lipid recovery for biofuel production. Bioresource Technology, 304, 122996. https://doi.org/10.1016/j.biortech.2020.122996
[3] Arnold, U., Brück, T., De Palmenaer, A., & Kuse, K. (2018). Carbon capture and sustainable utilization by algal polyacrylonitrile fiber production: process design, techno-economic analysis, and climate related aspects. Ind. Eng. Chem. Res., 57(23), 7922–7933. https://doi.org/10.1021/acs.iecr.7b04828
[4] TU München. (2019). Innovative Materialien mit Carbonfasern aus Algen. URL: https://www.ch.tum.de/ch/forschung/highlights/archiv-2019/innovative-materialien-mit-carbonfasern-aus-algen
[5] Darzins, A., Pienkos, P., & Edye, L. (2010). Current status and potential for algal biofuels production. A report to IEA Bioenergy Task, 39(13), 403–412.
[6] Sujan, A. R., Pang, S. H., Zhu, G., Jones, C. W., & Lively, R. P. (2019). Direct CO2 capture from air using poly(ethylenimine)-loaded polymer/silica fiber sorbents. ACS Sustainable Chem. Eng., 7(5), 5264–5273. https://doi.org/10.1021/acssuschemeng.8b06203
[7] Gambhir, A., & Tavoni, M. (2019). Direct air carbon capture and sequestration: how it works and how it could contribute to climate-change mitigation. One Earth, 1(4), 405–409. https://doi.org/10.1016/j.oneear.2019.11.006
[8] Lin, R., Guo, J., Li, X., Patel, P., & Seifitokaldani, A. (2020). Electrochemical reactors for CO2 conversion. Catalysts, 10(5), 473. https://doi.org/10.3390/catal10050473
[9] Ren, J., Li, F.-F., Lau, J., González-Urbina, L., & Licht, S. (2015). One-Pot Synthesis of Carbon Nanofibers from CO2. Nano Lett., 15(9), 6142–6148. https://doi.org/10.1021/acs.nanolett.5b02427
[10] Zuraiqi, K., Zavabeti, A., Clarke-Hannaford, J., Murdoch, B. J., Shah, K., Spencer, M. J. S., McConville, C. F., Daeneke, T., & Chiang, K. (2022). Direct conversion of CO2 to solid carbon by Ga-based liquid metals. Energy & Environmental Science, 15(2), 595–600. https://doi.org/10.1039/D1EE03283F
[11] Mili, M., Hashmi, S. A. R., Ather, M., Hada, V., Markandeya, N., Kamble, S., Mohapatra, M., Rathore, S. K. S., Srivastava, A. K., & Verma, S. (2022). Novel lignin as natural‐biodegradable binder for various sectors—A review. Journal of Applied Polymer Science, 139(15), 51951. https://doi.org/10.1002/app.51951
[12] Behr, A., & Seidensticker, T. (2018). Einführung in die Chemie nachwachsender Rohstoffe: Vorkommen, Konversion, Verwendung. https://doi.org/10.1007/978-3-662-55255-1
[13] Frank, E., Steudle, L. M., Ingildeev, D., Spörl, J. M., & Buchmeiser, M. R. (2014). Carbonfasern: Präkursor-Systeme, Verarbeitung, Struktur und Eigenschaften. Angew. Chem., 126(21), 5364–5403. https://doi.org/10.1002/ange.201306129
[14] Wang, S., Bai, J., Innocent, M. T., Wang, Q., Xiang, H., Tang, J., & Zhu, M. (2022). Lignin-based carbon fibers: Formation, modification and potential applications. Green Energy & Environment, 7(4), 578–605. https://doi.org/10.1016/j.gee.2021.04.006
[15] Black, S. (2016). Alternative precursor R&D: What are the alternatives to PAN? URL: https://www.compositesworld.com/articles/alternative-precursor-rd-what-are-the-alternatives-to-pan
[16] Zhang, D. (1993). Carbon fibers from oriented polyethylene precursors. Journal of Thermoplastic Composite Materials, 6(1), 38–48. https://doi.org/10.1177/089270579300600104
[17] Eun, J. H., & Lee, J. S. (2021). Study on polyethylene-based carbon fibers obtained by sulfonation under hydrostatic pressure. Sci Rep, 11(1), 18028. https://doi.org/10.1038/s41598-021-97529-4
[18] Zhang, D., & Sun, Q. (1996). Structure and properties development during the conversion of polyethylene precursors to carbon fibers. J. Appl. Polym. Sci., 62(2), 367–373. https://doi.org/10.1002/(SICI)1097-4628(19961010)62:2<367::AID-APP11>3.0.CO;2-Z
[19] Yaqoob, L., Noor, T., & Iqbal, N. (2022). Conversion of plastic waste to carbon-based compounds and application in energy storage devices. ACS Omega, 7(16), 13403–13435. https://doi.org/10.1021/acsomega.1c07291
[20] Marcilla, A., Ruiz-Femenia, R., Hernández, J., & García-Quesada, J. C. (2006). Thermal and catalytic pyrolysis of crosslinked polyethylene. Journal of Analytical and Applied Pyrolysis, 76(1–2), 254–259. https://doi.org/10.1016/j.jaap.2005.12.004
[21] Fraunhofer Institute for Applied Polymer Research IAP. (2019). Bio-based carbon fibers – high performance and sustainability for light-weight applications. URL: https://www.iap.fraunhofer.de/en/press_releases/2019/biobased-carbon-fibers.html
[22] Milbrandt, A., & Booth, S. (2016). Carbon fiber from biomass. Clean Energy Manufacturing Analysis Center (CEMAC). URL: https://www.nrel.gov/docs/fy16osti/66386.pdf
Zur Partnerschaft
Seien Sie Teil des Bündnisses und stellen Sie sich mit uns gemeinsam den Herausforderungen in Hinblick auf den nicht mehr zu vermeidenden Umgang mit Faserverbundwerkstoffen. Lassen Sie uns gemeinsam die Region „Elbtal Sachsen“ in eine wirtschaftlich widerstandsfähige Zukunft führen.