
Historical digression – a brief historical summary
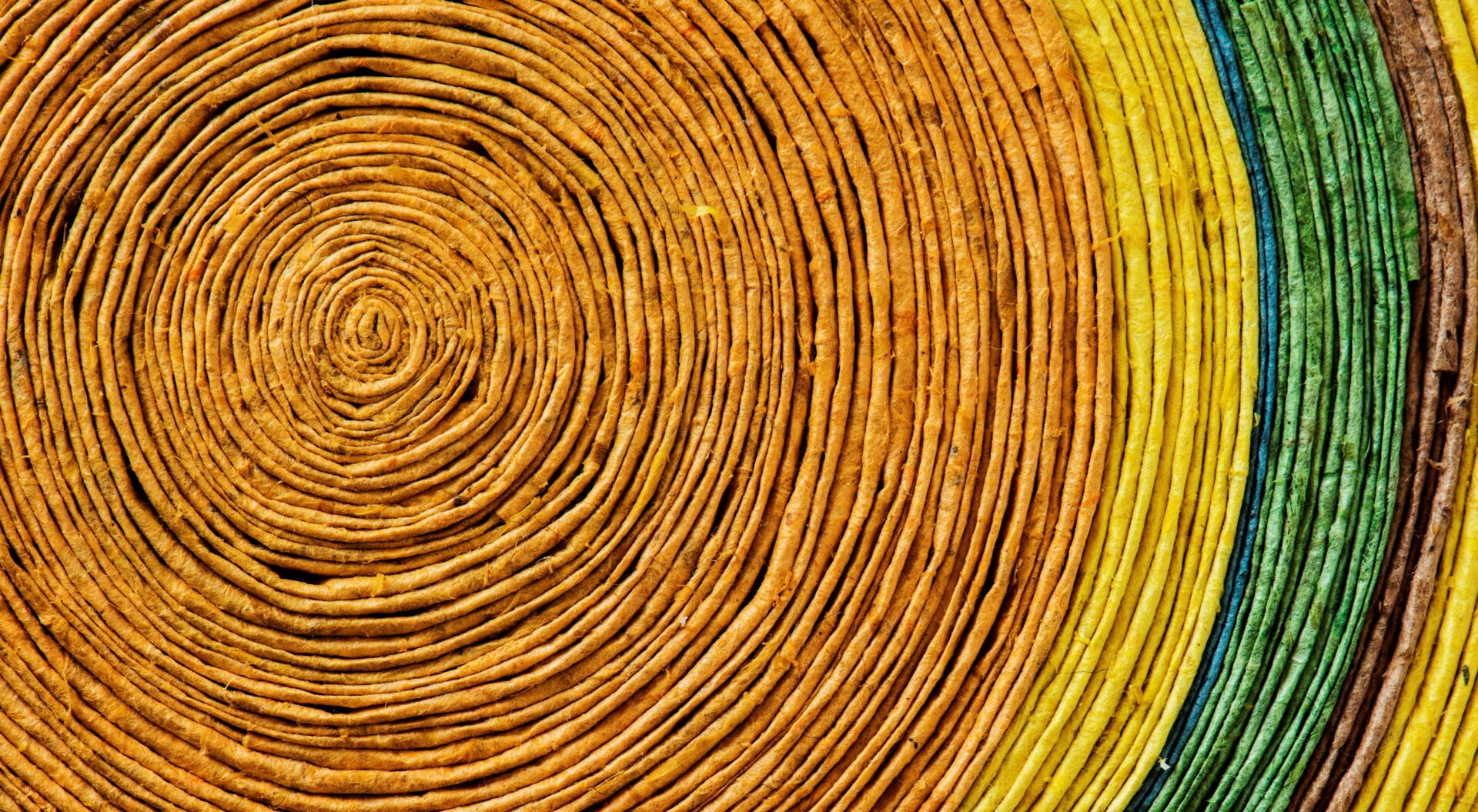
Natural inspiration
The plant and animal world stands out because structural set-ups are optimally adapted to fulfil the actual function. The advantages of a fibre-reinforced structure are so decisive that this completely dominates nature [1]. Fibre-reinforced structures can thus be found in the supporting structure of plants, muscles and bones [1, 2].
First applications
Humans have understood how to use fibre-reinforced structures made of natural materials such as bamboo, flax, hemp, silk, sisal, animal skins, wool and hair to make their clothing, tools and weapons since ancient times [2]. Early Egyptians and Mesopotamian settlers constructed their buildings using a composite mixture of clay and straw as early as 1,500 B.C. [3]. At this time, straw was also used to reinforce ancient pottery and boats.
Around 1,200 B.C., the Mongols invented the first bow, which was made from a combination of wood, bone and animal glue [3]. Until the invention of gunpowder, these bows were considered to be the most powerful weapon in the world due to their very high performance and precision, and propelled Genghis Khan to military supremacy [3, 4]. In the same century, the use of near-natural fibre composites was probably also written down for the first time. As the book of Exodus, chapter 5, verse 7, states: “You shall no longer give the people straw to make bricks! They must go and gather their own” [5].
Modern fibre composite materials
The modern era of fibre composite materials began with the production of polymers. In the 1900s, synthetic polymers such as vinyl, polystyrene, phenol and polyester were discovered. On account of their low material strength, polymers were initially not able to fulfil certain applications such as the load-bearing parts of cars, planes, sports equipment and wind turbine blades, which led to the specific implementation of reinforcements [6].
This was followed by great advances in development, since the advantages of fibre composite materials for the aviation and aerospace industry were obvious. Both industry and the military were quick to recognise that planes and helicopters could be built even lighter, allowing more cargo and weapons to be transported. In addition, greater manoeuvrability was achieved without impairing stability [7].
As development continued, more and more property rights were registered. The most important official registrations on the testing, production and use of fibre composites include [8]:
1907 | Patent for the production of phenol resins (“Bakelit”) for L. H. Baekland |
1916 | Patent for the production of a plane made completely of fibre-reinforced plastics for R. Kemp |
1935 | Start of the large-scale industrial production of glass fibres at Owens-Corning Fiberglas Corporation (USA) |
1938 | Patent for the production of epoxy resins (P. Castan) |
1942 | First components made of unsaturated polyester resin (UP)/glass fibres for planes, boats and cars |
1943 | First sandwich components for planes made of polyester resin/glass fibre and balsa wood for support |
1944 | Development and successful test flights with a fuselage produced using a GRP/sandwich method |
1945 | Production of honeycombs, a light and pressure-resistant core material for sandwich structures (L.S. Meyer) and development of the fibre winding method (G. Lubin and W. Greenberg) |
1951 | First pultrusion patent (extrusion method for producing profiles) and patenting of allylsilane glass coatings, the precursors of today’s silane adhesion promoters (R. Steinmann) |
1953 | Start of production of GF-UP (glass fibre/polyester resin) exterior parts for cars (Chevrolet Corvette) and development of the first GRP gliders in Germany |
1959 | Start of production of carbon fibres at Union-Carbide (USA) |
1967 | Test flights of the first plane made almost completely of GRP (Windecker Research Inc.) |
1971 | Start of production of aramid fibres (DuPont) under the brand name “Kevlar” |
1999 | Start of fundamental research on carbon concrete within the context of two special research areas – SB 528 and SFB 532 – funded by the German Research Association (Deutsche Forschungsgemeinschaft DFG) which gave rise to several property rights |
2014 | Start of user-oriented research and development work within the context of the C³ – Carbon Concrete Composite – project funded by the Federal Ministry of Education and Research (BMBF), which gave rise to several property rights |
2022 | The world’s first building made of carbon concrete is opened in Dresden |
As the use of fibre composite materials increased, the prices for raw materials and technologies dropped from 1,500 €/kg initially [9] to 15 €/kg today. As the price fell, the number of applications increased. In the meantime, the spectrum ranges from ultralight glasses frames through household and leisure equipment to applications in the wind power, automotive, shipbuilding, aviation and aerospace industries.
Near-natural future
As the use of carbon fibres increases, so does responsibility with regard to sustainable use. Inspired once again by nature, research is currently being conducted into the extraction of carbon fibres from algae [10], CO2 [11], lignin [12] or even polyethylene [13] so that carbon fibres will no longer have to be produced on the basis of crude oil in future.
As of 2023-10-06
List of references
[1] Drechsler, K., Karb, I., Kehrle, R., & Witzel, V. (2007). Faserverbundstrukturen, Themenheft Forschung, (3).
[2] Schürmann, H. (2007). Konstruieren mit Faser-Kunststoff-Verbunden. https://doi.org/10.1007/978-3-540-72190-1
[3] Nagavally, R. R. (2016). Composite materials-history, types, fabrication techniques, advantages, and applications. International Journal of Current Research, 8(9), 37763–37768
[4] Loades, M. (2016). The composite bow. Bloomsbury Publishing.
[5] Marom, G. (2021). The biomimetic evolution of composite materials: from straw bricks to engineering structures and nanocomposites. J. Compos. Sci., 5(5), 123. https://doi.org/10.3390/jcs5050123
[6] Vigneshwaran, S., Sundarakannan, R., John, K. M., Joel Johnson, R. D., Prasath, K. A., Ajith, S., Arumugaprabu, V., & Uthayakumar, M. (2020). Recent advancement in the natural fiber polymer composites: A comprehensive review. Journal of Cleaner Production, 277, 124109. https://doi.org/10.1016/j.jclepro.2020.124109
[7] Hahn, D., Kuhfeld, M., & Kreimer, L. (2014). Von Einbaum zum High-Tech-Sportgerät und die Geschichte der Faserverbundwerkstoffe. Technisches Gymnasium der Jörg-Zürn-Gewerbe-Schule.
[8] Ehrenstein, G. W. (2006). Faserverbund-Kunststoffe: Werkstoffe – Verarbeitung – Eigenschaften (2nd ed.).
[9] R&G Composite-Wiki. (2022). Kohlefaser (Carbon). URL: https://www.r-g.de/wiki/Kohlefasern_(Carbon)
[10] TU München. (2019). Innovative Materialien mit Carbonfasern aus Algen. Fakultät für Chemie, TUM.
[11] Lin, R., Guo, J., Li, X., Patel, P., & Seifitokaldani, A. (2020). Electrochemical reactors for CO2 conversion. Catalysts, 10(5), 473. https://doi.org/10.3390/catal10050473
[12] Wang, S., Bai, J., Innocent, M. T., Wang, Q., Xiang, H., Tang, J., & Zhu, M. (2022). Lignin-based carbon fibers: Formation, modification and potential applications. Green Energy & Environment, 7(4), 578–605. https://doi.org/10.1016/j.gee.2021.04.006
[13] Yaqoob, L., Noor, T., & Iqbal, N. (2022). Conversion of plastic waste to carbon-based compounds and application in energy storage devices. ACS Omega, 7(16), 13403–13435. https://doi.org/10.1021/acsomega.1c07291
About the partnership
Be part of the alliance and join us in facing the challenges with regard to the no longer avoidable handling of fibre composites. Let us together lead the region “Elbe Valley Saxony” into an economically resilient future.