
Approaches to recovery – The foundation has already been laid
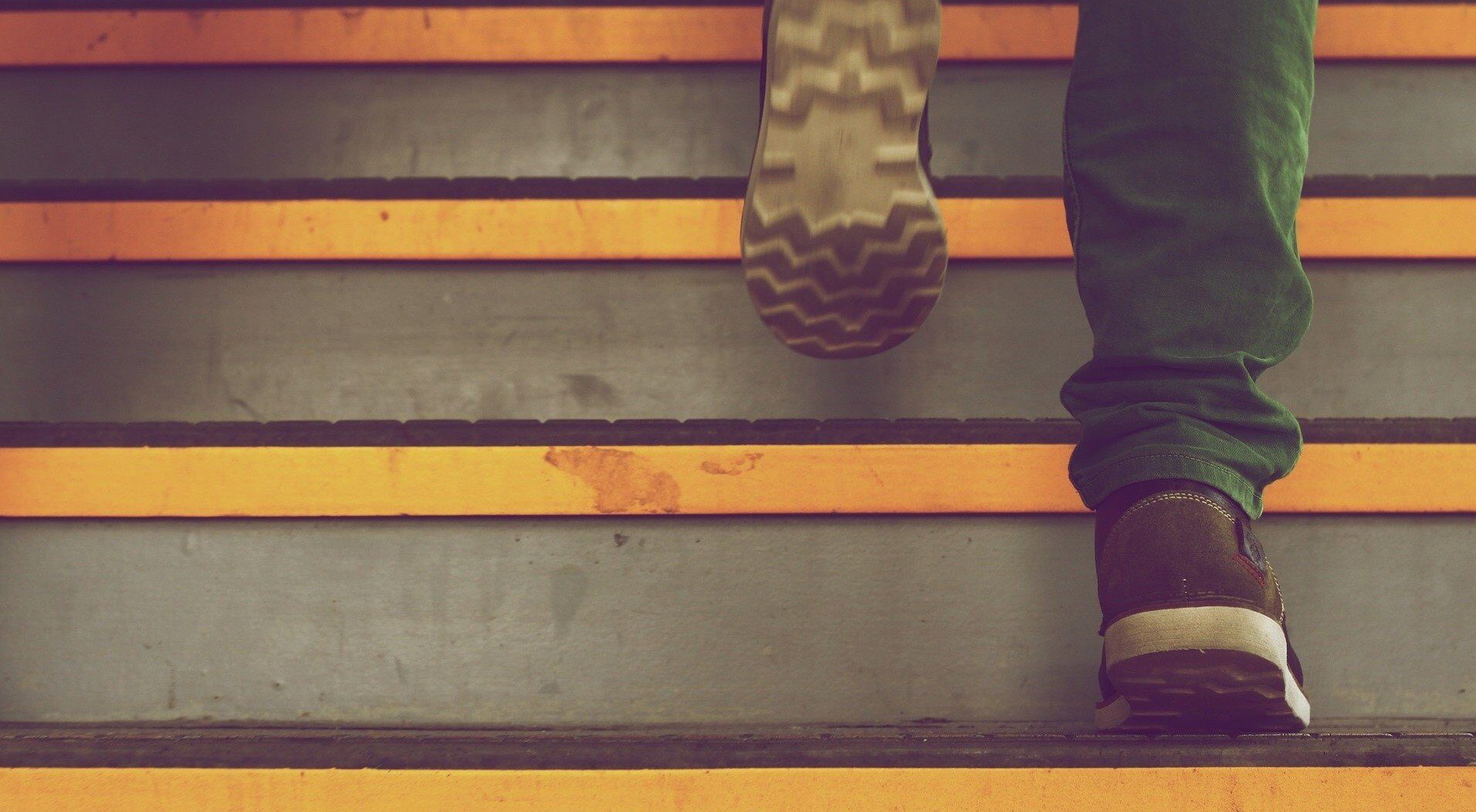
ReLei, project duration: 12/2014 to 05/2018
The Institute of Lightweight Engineering and Polymer Technology at the TU Dresden, the Institut für Aufbereitungsmaschinen der TU Freiberg (Institute for Processing Machinery at TU Freiberg) and the company ImpusTec from Radebeul played a major role in the implementation of the project. The goal of the project was the integrative development and production of a component made of recycled carbon fibres for use in the automotive sector. At the institute, it was possible to design an all-round approach for the construction of a fibre-reinforced component with maximum integration of recycled fibres. The demonstrator component manufactured in the project contains 80 % secondary raw materials, i.e. recycled fibres and plastics. To achieve this, attention was paid to the appropriate manufacturing processes for recycled raw materials during the component design phase. In addition, attention was paid to dismantling with regard to the separability of the materials used, so that the component can be recycled again after it has reached end-of-life status [1], [2].
VliesRTM, project run-time: 01/2017 to 12/2019
The project was carried out by the Fraunhofer Institute for Chemical Technology and the Sächsischen Textilforschungsinstitut (STFI) (Saxon Textile Research Institute). The research project focussed on the production and further processing of nonwovens from recycled carbon fibres under the aspect of cost optimisation and resource efficiency in different manufacturing processes. Non-infiltrated offcuts as well as fibres recovered through pyrolysis were used for the tests. The nonwovens produced can be used, for example, in vehicle and ship-building or in plant engineering in general. Especially for manufacturers of textile intermediate products made of carbon fibres, the process represents an opportunity to directly recycle their own waste. Over the last 15 years, the Saxon Textile Research Institute in Chemnitz has carried out more than 20 projects in the field of carbon fibre recycling. The common goal of these projects is to close the gap between the recovery of carbon fibres and their actual use in high-tech products [3], [4].
CarbonRevive, project run-time: 04/2018 to 09/2019
The project was carried out in cooperation between the Technical University of Freiberg, the Technical University of Chemnitz and SiC Processing GmbH based in Bautzen. The project aimed to design and pilot a process for the complete material recycling of waste containing carbon fibres. First, production waste from the field of electromobility was shredded and sorted for this purpose. Simple separation processes were used to separate different factions that can be used as aggregates in metallurgy. Smaller plastic fractions containing carbon fibres were broken down further by grinding, and separated into plastic and fibre components. The resulting powder containing carbon fibre was processed and tested as a filler in plastic granulates. Potential applications for such plastics can be found in the aviation and aerospace industries. The individual process steps were successfully implemented on a pilot scale. The project is particularly interesting with regard to the processing of smaller waste fractions from carbon-fibre reinforced plastics, where the extraction of longer fibre components is no longer possible [5].
ReCaHit, project run-time: 01/2018 to 12/2020
The Fraunhofer Institute for Chemical Technology and Karlsruhe Institute of Technology researched the replacement of primary raw materials by rCF (recycled Carbon Fibre) thermoplastic hybrid yarns in innovative thermoplastic processing methods. It was demonstrated that a transfer of the new approaches to industrial scales is possible while retaining the material-specific properties. Due to the reproducibility, good mechanical properties and economic efficiency, a real alternative to the use of primary raw materials is thus available [6]. Within the project, two different injection moulding compounding technologies were used to produce complex shaped demonstrators from recycled carbon fibre hybrid yarns. Furthermore, feasibility studies were developed in technologies such as the SMC process, wet pressing and 3D skeleton winding technology which promote the acceptance of secondary raw materials for lightweight construction elements in industry [7].
PyReCa, project run-time: 07/2019 to 06/2022
The project partners involved are the Technical University of Freiberg, the company LuxChemtech, also from Freiberg, and the company Linn High Term. The aim of the project is to develop a process for the complete material recycling of carbon-fibre reinforced plastic waste. In the process, the matrix component of the waste is also to be made usable again and the process optimised in terms of the quality of the recovered carbon fibres and the energy input. For this purpose, the pyrolysis is accelerated by using microwaves and the gases released are collected. These are used in the chemical industry, for example. Thus, a holistic and less energy-intensive recycling of carbon-fibre reinforced plastic waste can be achieved. In the further course of the project, an entire process chain up to the production of textile products from the recovered fibres is to be established [6], [7].
As of 2021-07-12
Updated 2022-03-03
List of references
[1] TU Dresden. URL: https://tu-dresden.de/ing/maschinenwesen/ilk/das-institut/news/neue-aufgaben-fuer-alte-fasern
[2] Forel. URL: https://plattform-forel.de/relei-bericht
[3] STFI Chemnitz. Abschlussbericht rCF-TFS Organobleche.
[4] STFI Chemnitz. URL: https://www.stfi.de/fileadmin/mediamanager/stfi/STFI/Dateien/5_Aktuelles/1_Publikationen/Newsletter20_2_web.pdf
[5] DBU. Abschlussbericht. URL: https://www.dbu.de/OPAC/ab/DBU-Abschlussbericht-AZ-34400_01-Hauptbericht.pdf
[6] Franhofer ICT. Innovative Use of Raw Materials in Thermoplastic Processes Project RECA-HIT
[7] Fraunhofer ICT Facebook. URL: https://www.facebook.com/FraunhoferICT
[8] Projektträger Jülich. URL: https://www.enargus.de/pub/bscw.cgi/?op=enargus.eps2&q=“01186250/1
[9] Bergakademie TU Freiberg. URL: https://tu-freiberg.de/sites/default/files/media/professur-fuer-gas–und-waermetechnische-anlagen-15258/pyreca_0.pdf
About the partnership
Be part of the alliance and join us in facing the challenges with regard to the no longer avoidable handling of fibre composites. Let us together lead the region “Elbe Valley Saxony” into an economically resilient future.