
Historischer Exkurs – ein geschichtlicher Abriss
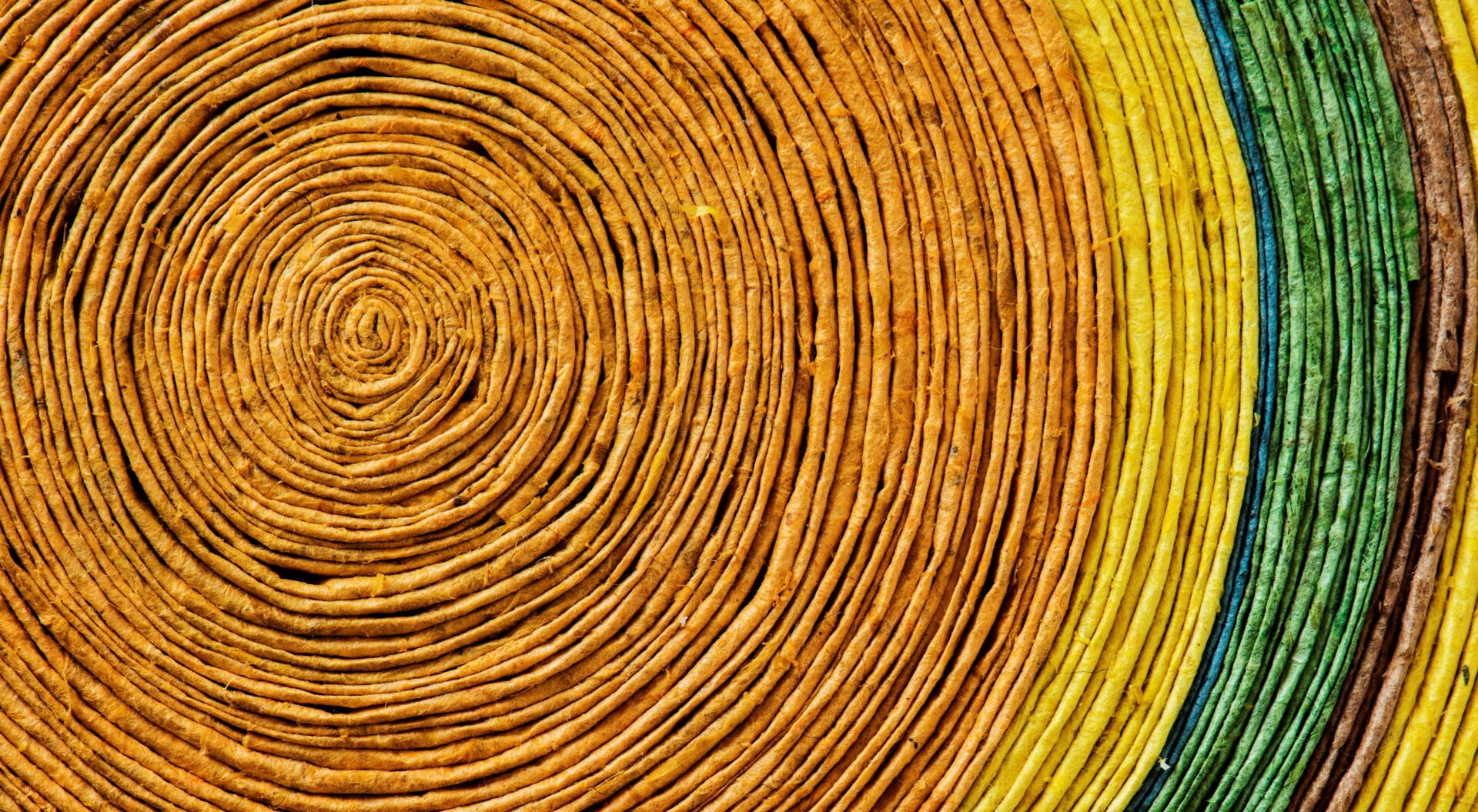
Natürliche Inspiration
Die Pflanzen- und Tierwelt zeichnet sich dadurch aus, dass der strukturelle Aufbau zur Erfüllung der eigentlichen Funktion optimal angepasst ist. Die Vorzüge einer faserverstärkten Struktur sind dabei so entscheidend, dass diese in der Natur absolut dominiert [1]. So finden sich faserverstärkte Strukturen beispielsweise in der Tragstruktur von Pflanzen, der Muskulatur und dem Knochenbau wieder [1, 2].
Erste Verwendungen
Der Mensch hat bereits seit der Antike verstanden, faserverstärkte Strukturen aus natürlichen Materialien wie Bambus, Flachs, Hanf, Seide, Sisal, Tierhäute, Wolle und Haaren zur Herstellung seiner Bekleidung, Werkzeuge und Waffen zu nutzen [2]. Als Verbund haben schon um 1.500 v. Chr. die frühen Ägypter und mesopotamischen Siedler ihre Gebäude mittels einer lehm- und strohhaltigen Mischung erbaut [3]. Zu dieser Zeit kam das Stroh auch zur Verstärkung alter Töpferwaren und Boote zu tragen.
Etwa 1.200 v. Chr. erfanden die Mongolen den ersten Bogen, der aus einer Kombination von Holz, Knochen und Tierleim bestand [3]. Bis zur Erfindung des Schießpulvers galten diese Bögen aufgrund ihrer sehr hohen Leistungsfähigkeit und Präzession als die stärkste Waffe der Welt, was Dschingis Khan zur militärischen Vorherrschaft verschaffte [3, 4]. Im selben Jahrhundert wurde der Einsatz von naturnahen Faserverbundwerkstoffen vermutlich auch zum ersten Mal verschriftlich. So ist im Buch Exodus 5:7 niedergeschrieben: „Gebt den Leuten nicht mehr, wie bisher, Stroh zum Ziegelmachen! Sie sollen selber gehen und sich Stroh besorgen“ [5].
Moderner Faserverbundwerkstoffe
Mit der Herstellung von Kunststoffen begann schließlich die moderne Ära der Faserverbundwerkstoffe. In den 1900er Jahren wurden synthetische Kunststoffe wie Vinyl, Polystyrol, Phenol und Polyester entdeckt. Aufgrund ihrer geringen Festigkeit konnten Kunststoffe bestimmte Anwendungen wie lastübertragende Teile von Autos, Flugzeugen, Sportgeräten und Windturbinenflügeln noch nicht erfüllen, wodurch gezielt Verstärkungen implementiert wurden [6].
Es folgten große Sprünge bei der Entwicklung, da die Vorteile der Faserverbundwerkstoffe für die Luft- und Raumfahrtindustrie auf der Hand lagen. Sowohl die Industrie als auch das Militär erkannten sehr schnell, dass Flugzeuge und Hubschrauber noch leichter gebaut werden konnten, wodurch wiederum mehr Ladung und Waffen transportiert werden konnten. Hinzu kam eine höhere Wendigkeit für Flugmanöver, ohne dabei die Stabilität zu beeinträchtigen [7].
Mit der anhaltendenden Entwicklung wurden auch immer mehr Schutzrechte angemeldet. Zu den wichtigsten offiziellen Registrierungen über die Prüfung, Herstellung und Verwendung von Faserverbundwerkstoffen zählen [8]:
1907 | Patent zur Herstellung von Phenolharzen („Bakelit“) an L. H. Baekland |
1916 | Patent über die Herstellung eines vollständig aus faserverstärkten Kunststoffen bestehenden Flugzeugs an R. Kemp |
1935 | Beginn der großtechnischen Herstellung von Glasfasern bei der Owens-Corning Fiberglas Corporation (USA) |
1938 | Patent zur Herstellung von Epoxydharzen (P. Castan) |
1942 | Erste Bauteile aus ungesättigtem Polyesterharz (UP)/Glasfaser für Flugzeuge, Boote und Autos |
1943 | Erste Sandwichbauteile für Flugzeuge aus Polyesterharz/Glasfasern und Balsaholz als Stützstoff |
1944 | Entwicklung und erfolgreiche Flugerprobung eines Flugzeugrumpfes, der in einer GFK/Sandwichbauweise hergestellt wurde |
1945 | Produktion von Wabenkernen (Honeycombs), eines leichten und druckfesten Kernmaterials für Sandwichkonstruktionen (L.S. Meyer) und Entwicklung des Faserwickelverfahrens (G. Lubin und W. Greenberg) |
1951 | Erstes Pultrusionspatent (Strangziehverfahren zur Herstellung von Profilen) und Patentierung von Allylsilan-Glasschlichten, den Vorläufern der heutigen Silan-Haftvermittler (R. Steinmann) |
1953 | Produktionsbeginn von GF-UP (Glasfaser/Polyesterharz) -Außenteilen im Automobilbau (Chevrolet Corvette) und Entwicklung der ersten GFK-Segelflugzeuge in Deutschland |
1959 | Produktionsbeginn von Kohlenstoffasern bei der Union-Carbide (USA) |
1967 | Flugerprobung des ersten, fast vollständig aus GFK hergestellten Flugzeuges (Windecker Research Inc.) |
1971 | Produktionsbeginn von Aramidfasern (DuPont) unter dem Markennamen „Kevlar“ |
1999 | Start der Grundlagenforschung zum Carbonbeton im Rahmen zweier durch das DFG geförderten Sonderforschungsbereiche SFB 528 und SFB 532, woraufhin mehrere Schutzrechte hervorgingen |
2014 | Start der anwenderorientierten Forschungs- und Entwicklungsleistungen im Rahmen des durch das BMBF geförderten Projektes C³ – Carbon Concrete Composite, woraufhin mehrere Schutzrechte hervorgingen |
2022 | Eröffnung des weltweit ersten Gebäudes aus Carbonbeton in Dresden |
Mit dem zunehmenden Einsatz von Faserverbundwerkstoffen sanken auch die Preise für Rohstoffe und Technologien von anfangs 1.500 EUR pro Kilo [9] auf gegenwärtige 15 EUR pro Kilo. Mit fallendem Preis nahm wiederum die Zahl der Anwendungen zu. Mittlerweile reicht das Spektrum von ultraleichten Brillengestellen über Haushalts- und Freizeitgeräte bis hin zum Einsatz in der Windkraftenergie, Automobil-, Schiffs-, Luft- und Raumfahrtindustrie.
Naturnahe Zukunft
Mit dem zunehmenden Einsatz von Kohlenstofffasern wächst auch die Verantwortung hinsichtlich eines nachhaltigen Umgangs. Wieder einmal durch die Natur inspiriert, wird gegenwärtig an der Gewinnung von Kohlenstofffasern aus Algen [10], CO2 [11], Lignin [12] oder gar Polyethylen [13] geforscht, um Kohlenstofffasern künftig nicht mehr auf Basis von Erdöl herstellen zu müssen.
Stand 2023-10-06
Quellenverzeichnis
[1] Drechsler, K., Karb, I., Kehrle, R., & Witzel, V. (2007). Faserverbundstrukturen, Themenheft Forschung, (3).
[2] Schürmann, H. (2007). Konstruieren mit Faser-Kunststoff-Verbunden. https://doi.org/10.1007/978-3-540-72190-1
[3] Nagavally, R. R. (2016). Composite materials-history, types, fabrication techniques, advantages, and applications. International Journal of Current Research, 8(9), 37763–37768
[4] Loades, M. (2016). The composite bow. Bloomsbury Publishing.
[5] Marom, G. (2021). The biomimetic evolution of composite materials: from straw bricks to engineering structures and nanocomposites. J. Compos. Sci., 5(5), 123. https://doi.org/10.3390/jcs5050123
[6] Vigneshwaran, S., Sundarakannan, R., John, K. M., Joel Johnson, R. D., Prasath, K. A., Ajith, S., Arumugaprabu, V., & Uthayakumar, M. (2020). Recent advancement in the natural fiber polymer composites: A comprehensive review. Journal of Cleaner Production, 277, 124109. https://doi.org/10.1016/j.jclepro.2020.124109
[7] Hahn, D., Kuhfeld, M., & Kreimer, L. (2014). Von Einbaum zum High-Tech-Sportgerät und die Geschichte der Faserverbundwerkstoffe. Technisches Gymnasium der Jörg-Zürn-Gewerbe-Schule.
[8] Ehrenstein, G. W. (2006). Faserverbund-Kunststoffe: Werkstoffe – Verarbeitung – Eigenschaften (2nd ed.).
[9] R&G Composite-Wiki. (2022). Kohlefaser (Carbon). URL: https://www.r-g.de/wiki/Kohlefasern_(Carbon)
[10] TU München. (2019). Innovative Materialien mit Carbonfasern aus Algen. Fakultät für Chemie, TUM.
[11] Lin, R., Guo, J., Li, X., Patel, P., & Seifitokaldani, A. (2020). Electrochemical reactors for CO2 conversion. Catalysts, 10(5), 473. https://doi.org/10.3390/catal10050473
[12] Wang, S., Bai, J., Innocent, M. T., Wang, Q., Xiang, H., Tang, J., & Zhu, M. (2022). Lignin-based carbon fibers: Formation, modification and potential applications. Green Energy & Environment, 7(4), 578–605. https://doi.org/10.1016/j.gee.2021.04.006
[13] Yaqoob, L., Noor, T., & Iqbal, N. (2022). Conversion of plastic waste to carbon-based compounds and application in energy storage devices. ACS Omega, 7(16), 13403–13435. https://doi.org/10.1021/acsomega.1c07291
Zur Partnerschaft
Seien Sie Teil des Bündnisses und stellen Sie sich mit uns gemeinsam den Herausforderungen in Hinblick auf den nicht mehr zu vermeidenden Umgang mit Faserverbundwerkstoffen. Lassen Sie uns gemeinsam die Region „Elbtal Sachsen“ in eine wirtschaftlich widerstandsfähige Zukunft führen.